Pneumatic Cylinder PU Piston Seal: A Comprehensive Guide
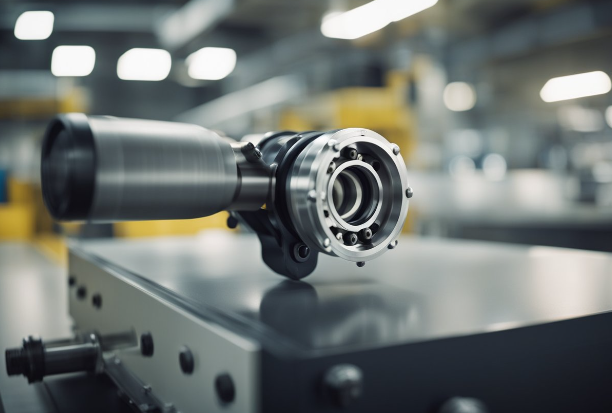
If you're working with pneumatic cylinders, then you know how important it is to have the right seals in place. One of the most critical components of a pneumatic cylinder is the piston seal, which helps to maintain a tight seal between the piston and the cylinder bore. This is essential for ensuring that the cylinder operates smoothly and efficiently.
One type of piston seal that is commonly used in pneumatic cylinders is the PU piston seal. PU stands for polyurethane, which is a type of polymer that is known for its durability and resistance to wear and tear. PU piston seals are designed to withstand the high pressures and temperatures that are often present in pneumatic cylinders, making them an ideal choice for a wide range of applications. With the right PU piston seal in place, you can be confident that your pneumatic cylinder will operate smoothly and reliably, even in challenging conditions.
Fundamentals of Pneumatic Cylinders
Pneumatic cylinders are devices that convert compressed air into mechanical energy to create linear or rotary motion. They are widely used in various industrial applications, such as automation, packaging, and material handling. In this section, we will discuss the working principle and components of pneumatic cylinders.
Working Principle of Pneumatic Cylinders
The working principle of pneumatic cylinders is based on the conversion of potential energy stored in compressed air into kinetic energy. When compressed air is supplied to the cylinder, it enters the cylinder through a port and pushes the piston, which is connected to a rod. The rod moves in a linear motion, creating a force that can be used to move loads or perform work.
The direction of the force depends on the design of the cylinder. Single-acting cylinders create force in one direction, while double-acting cylinders create force in both directions. The force generated by the cylinder is proportional to the surface area of the piston and the pressure of the compressed air.
Components of Pneumatic Cylinders
Pneumatic cylinders consist of several components that work together to create motion. The main components of a pneumatic cylinder are:
- Cylinder Barrel: The cylinder barrel is the main body of the cylinder that contains the piston and the rod. It is usually made of aluminum or stainless steel and is available in various sizes and shapes.
- Piston: The piston is a cylindrical component that moves back and forth inside the cylinder barrel. It is usually made of polyurethane or rubber and is designed to create a seal with the cylinder barrel.
- Rod: The rod is connected to the piston and extends outside the cylinder barrel. It is usually made of hardened steel and is designed to transmit force to the load.
- End Caps: The end caps are attached to the cylinder barrel and provide a mounting surface for the cylinder. They are usually made of aluminum or stainless steel and are designed to create a seal with the cylinder barrel.
- Seals: Seals are used to prevent air leakage between the piston and the cylinder barrel. They are usually made of polyurethane or rubber and are designed to withstand high pressure and temperature.
Overall, pneumatic cylinders are simple and reliable devices that are widely used in various industrial applications. By understanding the working principle and components of pneumatic cylinders, you can select the right cylinder for your application and ensure optimal performance.
PU Piston Seals Overview
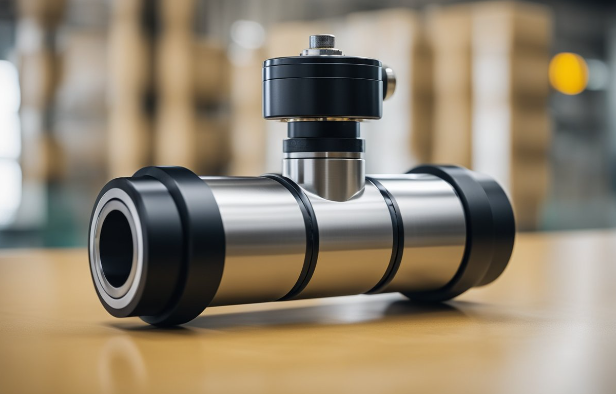
Characteristics of PU Seals
PU piston seals are a type of pneumatic cylinder seal made from polyurethane material. PU seals are known for their excellent wear resistance, high pressure resistance, and low friction coefficient. They are also resistant to chemicals, oil, and ozone, making them ideal for use in harsh environments.
PU piston seals have a high sealing efficiency, which means that they can maintain a tight seal even under high pressure. They are also able to withstand high temperatures, which makes them suitable for use in applications where heat is a factor.
PU piston seals come in a variety of sizes and shapes, which makes them adaptable to different types of pneumatic cylinders. They can be customized to meet the specific needs of your application, which makes them a versatile choice for a wide range of industries.
Advantages of Using PU Seals
There are several advantages to using PU piston seals in your pneumatic cylinder applications. Some of these advantages include:
- Excellent wear resistance: PU seals are known for their high wear resistance, which means that they can withstand the wear and tear of regular use without breaking down or losing their effectiveness.
- High pressure resistance: PU seals are able to withstand high pressure, which makes them ideal for use in applications where pressure is a factor.
- Low friction coefficient: PU seals have a low friction coefficient, which means that they can move smoothly and efficiently within the cylinder.
- Chemical and oil resistance: PU seals are resistant to chemicals and oil, which makes them ideal for use in harsh environments.
- Versatility: PU seals come in a variety of sizes and shapes, which makes them adaptable to different types of pneumatic cylinders.
Overall, PU piston seals are a reliable and durable choice for your pneumatic cylinder applications. With their excellent wear resistance, high pressure resistance, and low friction coefficient, they are sure to provide you with the sealing performance you need.
Design and Material Considerations
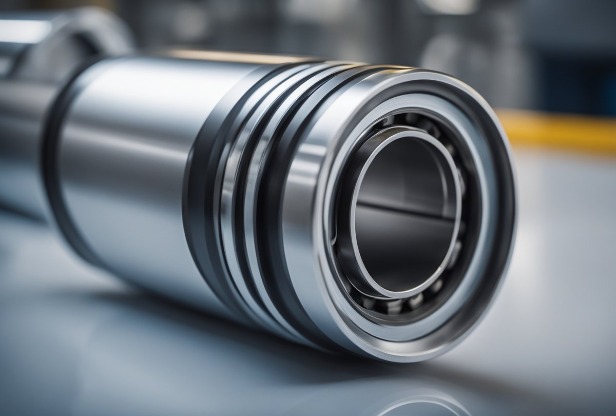
Material Properties of PU
Polyurethane (PU) is a versatile material with excellent mechanical properties, making it an ideal choice for pneumatic cylinder piston seals. PU exhibits high wear resistance, low friction, and good sealing performance. PU seals are also resistant to oil, grease, and most chemicals, making them suitable for a wide range of applications.
PU seals are available in different hardness levels, ranging from 70 Shore A to 95 Shore A. The choice of hardness depends on the application requirements, such as operating pressure, temperature, and speed. Harder seals are suitable for high-pressure applications, while softer seals are better for low-pressure applications.
Design Parameters for Seals
The design of pneumatic cylinder piston seals is critical for achieving optimal performance and reliability. The following design parameters should be considered when selecting and designing PU seals:
- Seal geometry: The seal geometry should be optimized for the specific application requirements, such as the cylinder bore and rod diameter, stroke length, and operating pressure. The seal geometry can have a significant impact on the sealing performance, friction, and wear.
- Lip design: The lip design of the seal should be optimized for the specific application requirements, such as the type of fluid, temperature, and speed. The lip design can have a significant impact on the sealing performance, leakage, and wear.
- Material selection: The material selection of the seal should be based on the specific application requirements, such as the type of fluid, temperature, and pressure. The material selection can have a significant impact on the sealing performance, chemical resistance, and wear.
- Installation: The installation of the seal should be performed according to the manufacturer's recommendations to ensure proper sealing performance and prevent damage to the seal.
In summary, the design and material considerations of pneumatic cylinder piston seals are critical for achieving optimal performance and reliability. PU is an excellent material choice for piston seals due to its mechanical properties, and the design parameters should be carefully considered to ensure proper sealing performance and prevent premature failure.
Installation and Maintenance
Proper Installation Techniques
Installing a pneumatic cylinder PU piston seal requires proper techniques to ensure optimal performance. Before installation, make sure that all the parts are clean and free of debris. Any dirt or debris can cause damage to the seal, leading to leaks and reduced efficiency.
When installing the seal, make sure that it is properly aligned with the cylinder. Misalignment can cause the seal to wear out quickly, leading to leaks and reduced performance. Use a seal installation tool to ensure that the seal is properly seated in the groove.
Make sure to apply lubrication to the seal and the cylinder before installation. Lubrication helps to reduce friction and wear, extending the life of the seal and the cylinder. Use a high-quality lubricant that is compatible with the seal material and the cylinder.
Maintenance and Troubleshooting
Regular maintenance is essential to ensure the optimal performance of the pneumatic cylinder PU piston seal. Check the seal regularly for signs of wear and tear, such as cracks, cuts, or deformation. Replace the seal immediately if you notice any signs of damage.
Check the cylinder for signs of leaks or damage. Leaks can occur due to worn-out seals or damaged cylinders. If you notice any leaks, check the seals and the cylinder for damage and replace them if necessary.
Regularly clean the cylinder and the seal to remove any dirt or debris that can cause damage. Use a soft cloth and a mild detergent to clean the parts. Avoid using harsh chemicals or abrasive materials that can cause damage to the seal and the cylinder.
In case of any issues with the pneumatic cylinder PU piston seal, troubleshoot the problem to identify the root cause. Check the seal and the cylinder for damage or misalignment. Replace the damaged parts and realign the cylinder to ensure optimal performance.
By following proper installation techniques and regular maintenance, you can ensure optimal performance of the pneumatic cylinder PU piston seal.
Applications and Industry Uses
Pneumatic cylinder PU piston seals are widely used in various industries due to their excellent sealing properties and durability. Here are some of the most common applications and industry uses of PU piston seals:
Automotive Industry
In the automotive industry, pneumatic cylinder PU piston seals are used in a variety of applications, including brake systems, shock absorbers, and suspension systems. These seals are designed to withstand high pressures and temperatures, making them ideal for use in harsh automotive environments.
Manufacturing Industry
The manufacturing industry relies heavily on pneumatics, and pneumatic cylinder PU piston seals are an essential component in many manufacturing processes. These seals are used in pneumatic cylinders to control the movement of machinery and equipment, ensuring smooth and accurate operation.
Medical Industry
PU piston seals are also used in the medical industry, where they are used in a variety of applications, including medical pumps and ventilators. These seals are designed to be hygienic and resistant to chemicals and bacteria, making them ideal for use in medical environments.
Aerospace Industry
In the aerospace industry, pneumatic cylinder PU piston seals are used in a variety of applications, including landing gear systems, wing flaps, and hydraulic actuators. These seals are designed to withstand extreme temperatures and pressures, making them ideal for use in the harsh conditions of space and aviation.
Overall, pneumatic cylinder PU piston seals are an essential component in many industries, providing reliable and long-lasting sealing solutions for a wide range of applications.