Polyurethane Buffer Seal: Benefits and Applications
If you work in an industry that relies on hydraulic systems, you may be familiar with the importance of buffer seals. These seals are designed to protect the primary rod seal from pressure spikes and other types of damage. One type of buffer seal that has become increasingly popular in recent years is the polyurethane buffer seal.
Polyurethane buffer seals are made from a thermoplastic material that is known for its resilience and resistance to wear. They are designed to provide reliable protection for hydraulic systems that operate under demanding conditions, including heavy loads and extreme pressure peaks. Polyurethane buffer seals are available in a range of profiles, including U-cup designs that feature both dynamic and static sealing lips.
If you're interested in learning more about polyurethane buffer seals, this article will provide an overview of the basics, including their design, manufacturing, and application in industry. We'll also cover installation and maintenance tips, as well as performance testing considerations. By the end of this article, you'll have a better understanding of how polyurethane buffer seals can benefit your hydraulic system and how to choose the right one for your needs.
Key Takeaways
- Polyurethane buffer seals are designed to protect primary rod seals from pressure spikes and other types of damage in hydraulic systems.
- These seals are made from a resilient thermoplastic material and are available in a range of profiles, including U-cup designs.
- When choosing a polyurethane buffer seal, it's important to consider factors such as the application, operating conditions, and performance testing requirements.
Polyurethane Buffer Seal Basics
Polyurethane buffer seals are an essential component of hydraulic systems that provide protection to the rod seals from high-pressure spikes. They are designed to withstand extreme pressure peaks and demanding workloads in heavy-duty applications. In this section, we will discuss the material composition and mechanical properties of polyurethane buffer seals.
Material Composition
Polyurethane buffer seals are made from a durable and tough urethane material that incorporates an anti-extrusion ring for high-pressure applications. The material composition of polyurethane buffer seals makes them resistant to wear, tear, and abrasion, which makes them ideal for use in harsh environments.
Mechanical Properties
Polyurethane buffer seals have a unique combination of mechanical properties that make them ideal for use in hydraulic systems. They have excellent compression set, which means they can withstand high-pressure spikes without losing their shape or form. They also have high tensile strength, which makes them resistant to tearing and breaking under high loads.
Another essential mechanical property of polyurethane buffer seals is their ability to maintain their sealing ability over a wide range of temperatures. They can withstand temperatures as low as -40°C and as high as 100°C, making them suitable for use in extreme temperature conditions.
In summary, polyurethane buffer seals are an essential component of hydraulic systems that protect the rod seals from high-pressure spikes. They are made from a durable and tough urethane material that incorporates an anti-extrusion ring for high-pressure applications. They have excellent compression set, high tensile strength, and can maintain their sealing ability over a wide range of temperatures.
Design and Manufacturing
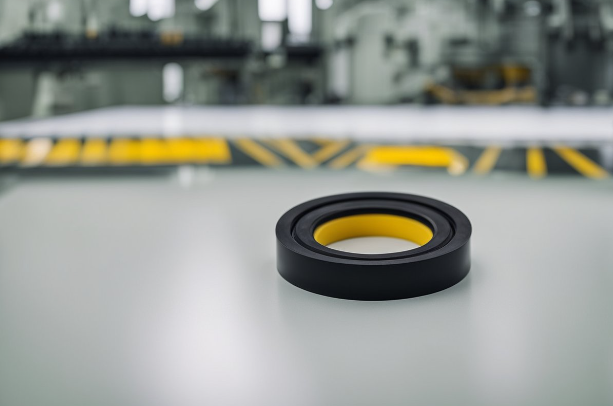
Seal Profiles
Polyurethane buffer seals are designed to prevent leakage of hydraulic fluid and to protect the primary seal from pressure spikes and contaminants. These seals are made of high-quality polyurethane material that provides excellent sealing performance and resistance to wear and tear.
There are several types of polyurethane buffer seal profiles available, including U-cups, V-rings, and piston seals. U-cup buffer seals are the most commonly used type of buffer seal due to their simple design and effective sealing performance. They consist of a U-shaped cross-section with a sealing lip that prevents fluid from leaking out of the cylinder.
V-ring buffer seals are designed to seal against a shaft or rod and are commonly used in applications where there are high-speed movements. Piston seals are used in applications where there is a reciprocating motion, and they are designed to prevent fluid from leaking past the piston.
Manufacturing Processes
Polyurethane buffer seals are manufactured using several different processes, including injection molding and compression molding. Injection molding is the most commonly used process for manufacturing buffer seals. It involves injecting molten polyurethane material into a mold cavity and allowing it to cool and solidify.
Compression molding is another process used for manufacturing buffer seals. It involves placing a preform of polyurethane material into a mold cavity and then compressing it under heat and pressure. This process is commonly used for manufacturing large buffer seals or seals with complex geometries.
In conclusion, the design and manufacturing of polyurethane buffer seals are critical to their sealing performance and durability. The selection of the appropriate seal profile and manufacturing process can greatly affect the overall performance of the seal.
Application in Industry
Polyurethane buffer seals are commonly used in various industries due to their high resistance to wear and tear, and their ability to withstand high pressure environments. In this section, we will explore the two main applications of polyurethane buffer seals in industry: hydraulic systems and pneumatic systems.
Hydraulic Systems
Hydraulic systems use polyurethane buffer seals in conjunction with primary rod seals to improve performance and withstand high pressure and system pressure spikes. The polyurethane buffer seal is designed to protect the primary rod seal from damage caused by pressure spikes. The buffer seal is o-ring energized, low friction, and extrusion-resistant, making it ideal for use in hydraulic systems.
Polyurethane buffer seals are also suitable for heavy-duty applications and extreme pressures. They have an improved gap extrusion resistance, which ensures that pressure can return to the system side of the buffer and prevents the build-up of pressure between the rod and buffer seals. These profiles are suitable for extreme pressure peaks and demanding workloads in heavy-duty applications up to 690 bar (10 000 psi).
Pneumatic Systems
Polyurethane buffer seals are also commonly used in pneumatic systems. They are designed to vent pressure back to the system side of the buffer and prevent the build-up of pressure between the rod and buffer seals. The flexible outside static sealing lip and notches in the front face safeguard that pressure can return to the system side of the buffer and prevent build-up of pressure between the rod and buffer seals.
Polyurethane buffer seals in pneumatic systems are also suitable for extreme pressure peaks and demanding workloads. They have excellent wear and rebound characteristics, making them ideal for use in pneumatic systems.
In conclusion, polyurethane buffer seals are widely used in industry due to their high resistance to wear and tear and their ability to withstand high pressure environments. They are commonly used in hydraulic and pneumatic systems to improve performance and prevent damage caused by pressure spikes.
Installation and Maintenance
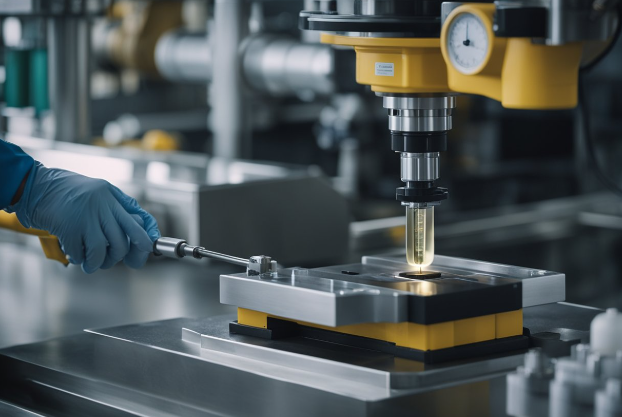
Installation Guidelines
Proper installation of polyurethane buffer seals is essential to ensure optimal performance. Before installation, make sure that the rod surface is clean and free of any dirt, debris, or damage. Any contaminants on the rod surface can lead to premature wear of the seal, resulting in leakage or failure.
To install the buffer seal, follow these steps:
- Lubricate the seal and the rod surface with a compatible lubricant. This will help to reduce friction during installation and ensure a proper fit.
- Carefully slide the seal onto the rod, making sure that it is seated properly.
- Use a seal installation tool to press the seal into place. Be sure to apply pressure evenly around the circumference of the seal to avoid damaging it.
- Once the seal is installed, check for proper fit and make any necessary adjustments.
Maintenance Tips
Proper maintenance of polyurethane buffer seals can help to extend their lifespan and prevent premature failure. Here are some tips to keep in mind:
- Regularly inspect the seal for signs of wear or damage, such as cracks, tears, or distortion. Replace the seal if any of these issues are present.
- Check the rod surface for any signs of damage or corrosion. If the rod is damaged, it can cause premature wear of the seal.
- Keep the seal and the rod surface clean and free of any dirt or debris. This will help to prevent contamination and ensure proper sealing.
- Use a compatible lubricant to reduce friction and extend the life of the seal.
By following these installation and maintenance guidelines, you can ensure that your polyurethane buffer seals perform as intended and provide long-lasting, reliable sealing.
Performance and Testing
Durability Assessments
Polyurethane buffer seals are designed to withstand high pressure and temperature fluctuations, making them ideal for use in hydraulic systems. These seals undergo a series of tests to ensure their durability and performance. Some of the tests include:
- Pressure testing: The seals are tested under high pressure to ensure they can withstand the maximum pressure rating.
- Temperature testing: The seals are tested under extreme temperatures to ensure they can withstand the minimum and maximum temperature range.
- Abrasion testing: The seals are tested for abrasion resistance to ensure they can withstand wear and tear over time.
- Chemical resistance testing: The seals are tested for their resistance to various chemicals to ensure they can withstand exposure to different fluids.
Quality Standards
Polyurethane buffer seals are manufactured to meet certain quality standards to ensure their performance and reliability. Some of the quality standards include:
- ISO 9001: This standard ensures that the manufacturer has a quality management system in place to ensure consistent quality.
- ISO/TS 16949: This standard is specific to the automotive industry and ensures that the manufacturer meets certain quality requirements for automotive parts.
- ASTM D2000: This standard specifies the requirements for rubber and rubber-like materials used in seals and gaskets.
By meeting these quality standards, polyurethane buffer seals are able to provide reliable performance in hydraulic systems.