PU Oil Seal in IDI Type: A Comprehensive Guide
If you are in the market for a reliable oil seal for your hydraulic equipment, you may want to consider the PU oil seal in the IDI type. This type of seal is designed specifically for rod applications and is the most critical seal on any type of fluid power plant. Its primary function is to prevent fluid from leaking out of the cylinder to the outside, which is crucial for optimal equipment performance.
The PU oil seal in the IDI type is made of high-performance polyurethane elastomer with a hardness rating of 93 2 Shore A. It has a short internal seal lip that is designed to provide a secure fit and prevent leakage of fluids from within the cylinder to the outside. With a pressure rating of up to 400 Bar, a temperature range of -35 to +110 degrees Celsius, and a speed of 0.5m/s, this seal is suitable for a wide range of hydraulic applications.
Overall, the PU oil seal in the IDI type is a reliable and effective solution for preventing fluid leakage in hydraulic equipment. Its robust construction and high-performance materials make it an ideal choice for demanding industrial applications. If you are looking for a quality seal that can withstand high pressures, temperatures, and speeds, the PU oil seal in the IDI type is definitely worth considering.
Overview of PU Oil Seals
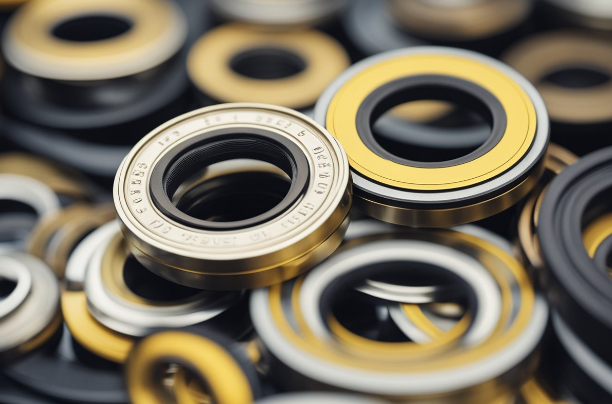
PU oil seals are a type of hydraulic seal used to prevent the leakage of fluids in hydraulic systems. They are made of polyurethane elastomers, which are known for their high abrasion resistance, toughness, and durability. PU oil seals are widely used in a variety of industrial applications, including hydraulic cylinders, machine tools, presses, and mobile machinery.
Material Properties
Polyurethane elastomers are highly versatile materials that offer a range of beneficial properties for use in hydraulic seals. Some of the key material properties of PU elastomers include:
- High Abrasion Resistance: PU elastomers are highly resistant to abrasion, making them ideal for use in hydraulic seals that are exposed to high levels of wear and tear.
- Toughness: PU elastomers are tough and resilient, enabling them to withstand high levels of stress and strain without cracking or breaking.
- Flexibility: PU elastomers are highly flexible, allowing them to conform to irregular surfaces and maintain a tight seal even under extreme conditions.
- Chemical Resistance: PU elastomers are resistant to a wide range of chemicals, including oils, fuels, and hydraulic fluids, making them ideal for use in hydraulic seals.
Advantages of PU Seals
PU oil seals offer a number of advantages over other types of hydraulic seals. Some of the key advantages of PU seals include:
- High Durability: PU seals are highly durable and can withstand high levels of wear and tear, making them ideal for use in industrial applications.
- Low Friction: PU seals have a low coefficient of friction, which helps to reduce energy consumption and improve the efficiency of hydraulic systems.
- Easy Installation: PU seals are easy to install and can be quickly and easily replaced when needed.
- Wide Temperature Range: PU seals can operate over a wide temperature range, making them suitable for use in both high and low temperature environments.
Overall, PU oil seals are a reliable and cost-effective solution for preventing fluid leakage in hydraulic systems. With their high durability, low friction, and ease of installation, PU seals are an excellent choice for a wide range of industrial applications.
IDI Type Seal Design
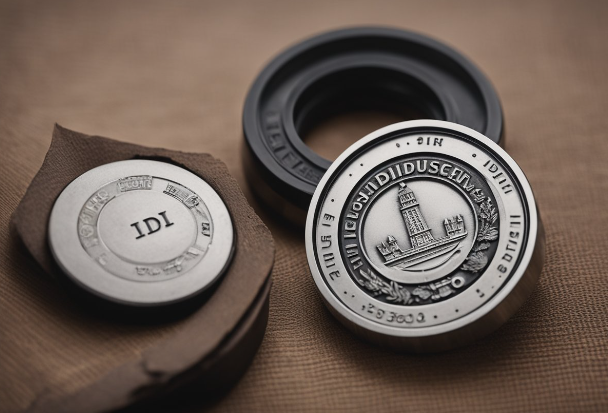
Seal Profile Characteristics
The IDI type seal is a U-cup seal with a single sealing lip that is shorter on the inside than on the outside. The asymmetrical lip design provides good sealing performance while minimizing friction and wear. The IDI seal is typically made of polyurethane (PU) elastomer, which has good resistance to wear, abrasion, and extrusion. The seal can be designed to operate in a wide range of temperatures and pressures, depending on the specific application requirements.
Application Suitability
The IDI type seal is suitable for use in hydraulic and pneumatic cylinders, where it is installed on the rod or piston to prevent fluid leakage to the outside of the cylinder. The seal is critical for maintaining the performance and reliability of the cylinder, as any leakage can reduce the efficiency and effectiveness of the system. The IDI seal is commonly used in mobile machinery, machine tools, presses, and standard cylinders.
When selecting an IDI type seal for your application, consider the following factors:
- Operating temperature and pressure range
- Fluid compatibility
- Rod or piston diameter and stroke length
- Speed and frequency of operation
- Environmental conditions, such as dust and debris
- Installation and assembly requirements
By carefully evaluating these factors and selecting the appropriate IDI type seal, you can ensure optimal performance and longevity of your hydraulic or pneumatic cylinder.
Manufacturing Process
Molding Techniques
The manufacturing process of PU oil seals in IDI type involves molding techniques that ensure the final product is of high quality. The molding techniques used include injection molding and compression molding.
Injection molding is the process of injecting molten material into a mold cavity, which then solidifies into the desired shape. This technique is used to produce high volume and complex parts with tight tolerances.
Compression molding, on the other hand, involves placing a preheated material into a heated mold cavity, then applying pressure to the material until it takes the shape of the mold. This technique is used to produce parts with higher strength and stiffness than injection molding.
Quality Control Standards
Quality control is an essential part of the manufacturing process of PU oil seals in IDI type. To ensure that the final product meets the required quality standards, various quality control measures are put in place.
One of the quality control measures used is the inspection of raw materials. The raw materials used in the production of PU oil seals are inspected to ensure that they meet the required specifications.
During the manufacturing process, the seals are also inspected at various stages to ensure that they meet the required specifications. This includes checking the dimensions, hardness, and surface finish of the seals.
Before the final product is released into the market, it undergoes a final inspection to ensure that it meets the required quality standards. This includes checking for defects such as cracks, tears, and deformities.
Overall, the manufacturing process of PU oil seals in IDI type involves molding techniques and quality control measures that ensure the final product is of high quality and meets the required specifications.
Installation Guidelines
Preparation Steps
Before installing your PU oil seal in IDI type, you need to ensure that you have all the necessary tools and equipment. This includes a clean work area, a lint-free cloth, and the appropriate installation tools. You should also have the manufacturer's installation instructions on hand for reference.
To prepare for installation, follow these steps:
- Clean the seal and installation tools thoroughly with a lint-free cloth. This helps prevent dust and solid particles from compromising the seal's functionality.
- Verify that the shaft surface is free from nicks, burrs, and scratches. Any surface imperfections can damage the seal and cause leaks.
- Lubricate the seal with system oil before installation.
Installation Procedures
To install your PU oil seal in IDI type, follow these procedures:
- Position the seal in the groove with the sealing lip facing inward. Ensure that the seal is properly seated in the groove.
- Use the appropriate installation tool to press the seal into place. Do not use a tool that can damage the seal or the shaft surface.
- Check that the seal is properly aligned and seated in the groove. Use a feeler gauge to verify that the seal is flush with the shaft surface.
- Apply a light coating of system oil to the seal lip and shaft surface to prevent dry running.
- Reinstall the housing or cover and tighten the bolts to the manufacturer's specifications.
By following these installation guidelines, you can ensure that your PU oil seal in IDI type is installed correctly and functions properly. If you have any questions or concerns about the installation process, consult the manufacturer's instructions or seek the assistance of a trained professional.
Maintenance and Troubleshooting
Routine Inspection
To ensure the longevity and proper functioning of your PU oil seal in IDI type, it is important to perform routine inspections. You should inspect your seals at least once a year, or more frequently if your equipment is subjected to harsh conditions. During the inspection, you should look for any signs of damage, such as cracks, tears, or wear. You should also check for any signs of leakage, which can indicate that the seal is not functioning properly.
To inspect your PU oil seal in IDI type, follow these steps:
- Clean the area around the seal to remove any dirt or debris.
- Look for any signs of damage or wear on the seal surface.
- Check for any signs of leakage around the seal.
- If you notice any issues, replace the seal immediately.
Performing routine inspections can help you catch and address any issues before they become major problems.
Common Issues and Solutions
Despite proper maintenance, your PU oil seal in IDI type may encounter issues. Here are some common issues and potential solutions:
- Leakage: If you notice any leakage around the seal, it could indicate that the seal is not functioning properly. This can be caused by a variety of factors, such as improper installation, damage to the seal surface, or wear. To address leakage, you may need to replace the seal or adjust the installation.
- Wear: Over time, your PU oil seal in IDI type may experience wear, which can cause it to fail. This can be caused by a variety of factors, such as exposure to harsh conditions or improper installation. To address wear, you may need to replace the seal or adjust the installation.
- Damage: Your PU oil seal in IDI type may become damaged due to exposure to harsh conditions or improper installation. Damage can manifest as cracks, tears, or other issues. To address damage, you may need to replace the seal or adjust the installation.
By identifying and addressing these common issues, you can ensure that your PU oil seal in IDI type continues to function properly and provide reliable performance.