PU Plastic Hydraulic Seal: Benefits and Applications
If you work with hydraulic systems, you know the importance of choosing the right seals to ensure optimal performance and longevity. One popular option is the PU plastic hydraulic seal, made from thermoplastic polyurethane (TPU). These seals are known for their excellent resilience, resistance to wear and extrusion, and ability to maintain a tight seal even under high pressure.
PU plastic hydraulic seals are commonly used in a variety of hydraulic applications, including cylinders, valves, and machine tools. They are ideal for high-pressure environments, where other seal materials may fail. Additionally, PU plastic hydraulic seals are resistant to a wide range of chemicals and can operate in both high and low temperatures.
When choosing a PU plastic hydraulic seal, it's important to consider factors such as the size and shape of the seal, the material it will be in contact with, and the specific operating conditions of your hydraulic system. With the right seal in place, you can ensure that your hydraulic system operates smoothly and efficiently, reducing the risk of downtime and costly repairs.
Overview of PU Plastic Hydraulic Seals
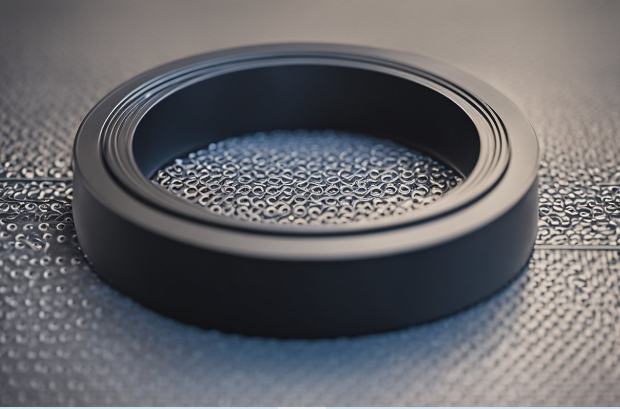
If you are looking for a reliable and durable sealing solution for your hydraulic system, PU plastic hydraulic seals are a great choice. These seals are made of a type of polyurethane material that offers excellent resistance to wear, tear, and chemical corrosion. In this section, we will provide an overview of PU plastic hydraulic seals, including their composition, properties, types, and applications.
Composition and Properties
PU plastic hydraulic seals are made of a type of polyurethane material that is known for its flexibility, strength, and durability. This material is composed of a long-chain polymer that is formed by the reaction of a diisocyanate with a polyol. The resulting material is then processed into various shapes and sizes, including hydraulic seals.
PU plastic hydraulic seals offer excellent resistance to wear, tear, and chemical corrosion. They are also highly resistant to temperature changes, making them suitable for use in a wide range of environments. Additionally, PU plastic hydraulic seals have a low compression set, which means they can maintain their sealing properties over a long period of time.
Types and Applications
There are several types of PU plastic hydraulic seals, including rod seals, piston seals, wipers, and buffer seals. Each type of seal is designed to perform a specific function within a hydraulic system. For example, rod seals are used to prevent leakage of fluid from the cylinder, while piston seals are used to prevent leakage of fluid from the piston.
PU plastic hydraulic seals are commonly used in a wide range of applications, including construction equipment, agricultural machinery, mining equipment, and industrial machinery. They are also used in hydraulic systems that are exposed to harsh environments, such as extreme temperatures, high pressure, and chemical exposure.
PU plastic hydraulic seals are an excellent choice for anyone looking for a reliable and durable sealing solution for their hydraulic system. With their excellent resistance to wear, tear, and chemical corrosion, as well as their low compression set and high temperature resistance, PU plastic hydraulic seals are sure to provide long-lasting performance and protection for your hydraulic system.
Manufacturing Processes
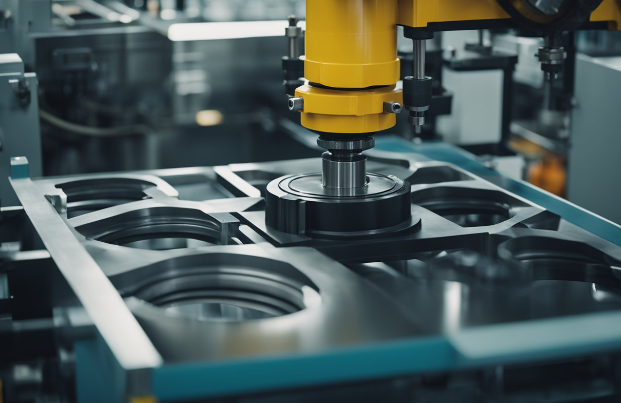
When it comes to manufacturing PU plastic hydraulic seals, there are two primary processes: injection molding and compression molding. Both processes have their advantages and disadvantages, and the choice of which to use will depend on a number of factors, including the size and complexity of the part, the desired production volume, and the cost of tooling.
Injection Molding
Injection molding is a popular manufacturing process for producing high-volume, complex parts with tight tolerances. The process involves heating plastic pellets until they melt, then injecting the molten plastic into a mold. The plastic then cools and solidifies, taking on the shape of the mold. Injection molding is ideal for parts with intricate geometries, such as hydraulic seals, and can produce parts with consistent quality and high repeatability.
Compression Molding
Compression molding is a process in which a preheated material is placed into a heated mold cavity and then compressed to shape the part. The heat and pressure cause the material to flow and fill the mold cavity, taking on its shape. Compression molding is ideal for low- to medium-volume production runs of parts with simple geometries. It is a cost-effective process that can produce parts with good dimensional accuracy and surface finish.
In summary, both injection molding and compression molding are viable options for manufacturing PU plastic hydraulic seals. The choice of which to use will depend on a number of factors, including the size and complexity of the part, the desired production volume, and the cost of tooling.
Performance Characteristics
Pressure Resistance
PU plastic hydraulic seals are designed to withstand high-pressure environments. The material's inherent toughness and flexibility allow it to maintain its shape and sealing properties even under extreme pressure. PU plastic hydraulic seals can handle pressures up to 5,000 PSI, making them ideal for use in heavy-duty hydraulic systems.
Temperature Tolerance
PU plastic hydraulic seals have a wide temperature range, making them suitable for use in both high- and low-temperature environments. PU plastic hydraulic seals can operate in temperatures ranging from -65°F to +275°F. This temperature range ensures that the seals remain effective even in harsh conditions.
Wear and Tear Resilience
PU plastic hydraulic seals are highly resistant to wear and tear, making them ideal for use in high-stress applications. They can withstand repeated use and exposure to harsh environments without losing their sealing properties. PU plastic hydraulic seals are also resistant to extrusion and compression set, ensuring that they maintain their shape and sealing properties over time.
In summary, PU plastic hydraulic seals are an excellent choice for use in heavy-duty hydraulic systems. They offer excellent pressure resistance, temperature tolerance, and wear and tear resilience, ensuring that they remain effective even in harsh conditions.
Installation and Maintenance
Installation Guidelines
When installing PU plastic hydraulic seals, it is important to follow certain guidelines to ensure proper functionality and longevity. Here are some guidelines to follow:
- Cleanliness is Key: Before installation, make sure the surfaces are clean and free of debris, dust, and other particles. Use a lint-free cloth to clean the seal and installation tools thoroughly. This helps prevent solid particles from compromising the seal's functionality.
- Lubrication is Important: Apply a thin layer of lubricant to the seal and the surface it will be installed on. This will help prevent damage to the seal during installation and ensure proper sealing function.
- Proper Installation Tools are Necessary: Use the correct installation tools for the job. Using the wrong tools can damage the seal, causing it to fail prematurely.
- Avoid Sharp Edges: Guard against sharp edges during installation. Sharp edges can cause damage to the seal and affect its performance.
Maintenance Best Practices
Maintaining your PU plastic hydraulic seals is crucial to ensure their longevity and proper function. Here are some best practices to follow:
- Inspect Regularly: Inspect your hydraulic seals regularly for any signs of damage or wear. Replace them immediately if you notice any damage or wear.
- Keep the System Clean: Keep your hydraulic system clean and free of debris. This will help prevent damage to the seals and other components.
- Use Proper Lubrication: Use the correct lubrication for your hydraulic system. Using the wrong lubrication can cause damage to the seals and other components.
- Monitor System Pressure: Monitor your hydraulic system pressure regularly. High pressure can cause damage to the seals and other components, leading to premature failure.
By following these installation and maintenance guidelines, you can ensure that your PU plastic hydraulic seals will function properly and last longer.
Quality and Compliance Standards
When it comes to PU plastic hydraulic seals, quality and compliance standards are of utmost importance to ensure that they perform reliably and safely. Here are some of the key standards and certifications that you should look for when selecting a supplier for your hydraulic seals.
ISO Standards
ISO (International Organization for Standardization) is an independent, non-governmental international organization that develops and publishes standards for various industries. When it comes to hydraulic seals, the ISO 9001 standard is particularly relevant. This standard specifies the requirements for a quality management system (QMS) and ensures that the supplier has a robust QMS in place to consistently provide products that meet customer and regulatory requirements.
Industry-Specific Certifications
In addition to ISO standards, there are also industry-specific certifications that hydraulic seal suppliers can obtain to demonstrate their commitment to quality and compliance. Some of the most common certifications include:
- AS9100: This is a quality management system standard specifically for the aerospace industry. It is based on the ISO 9001 standard but includes additional requirements specific to the aerospace industry.
- TS16949: This is a quality management system standard specifically for the automotive industry. It is based on the ISO 9001 standard but includes additional requirements specific to the automotive industry.
- FDA: This certification is required for hydraulic seals that come into contact with food, drugs, or medical devices. It ensures that the seals are made from materials that are safe for human consumption and that they are manufactured in a clean and controlled environment.
When selecting a supplier for your PU plastic hydraulic seals, it is important to ensure that they meet the relevant quality and compliance standards. This will give you peace of mind knowing that the seals you are using are safe, reliable, and meet the requirements of your industry.